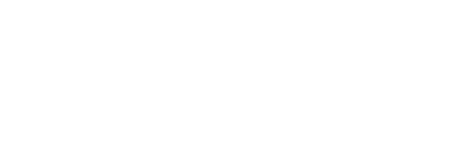
KMT is proud to be a Shape Technologies Group Company.
Shape Technologies Group, Inc. (SHAPE) delivers innovative manufacturing process solutions to customers spanning 100 countries and a broad array of industries. As the world leading provider and inventor of waterjet, SHAPE has become a strategic network of companies providing material processing and surface preparation, automated assembly, robotic motion systems, material handling, software, process control, aftermarket parts, and comprehensive support to our customers.